Plastic injection molding allows manufacturers to produce a large number of identical and dimensionally consistent products, which makes it ideal for high-volume productions that require exacting specifications. Proper design is crucial, including features such as threaded inserts, core pulls, and living hinges.
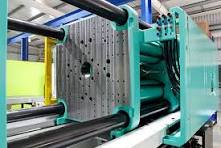
The type of steel alloy is also a major factor in mold durability, as it offers varying degrees of hardness and resistance to heat. Regular maintenance, including scheduled and predictive procedures, can also significantly boost an injection mold’s lifespan. Read on Plastic Injection Mold Florida for further details.
Thermoplastic polymers are commonly used in injection molding due to their flexibility. They can be melted, reshaped and cooled repeatedly without changing their chemical structure, which makes them ideal for parts with precise dimensional tolerances. They are also cost-effective to produce, making them the preferred material for high-volume production.
The key to producing high-quality thermoplastic injection molded parts is optimizing the injection process. Melt temperature, injection pressure and cooling are critical for ensuring quality results. The melt temperature directly influences the viscosity of the molten plastic, which impacts the ease with which it fills the mold cavity and replicates intricate design details. Injection pressure, which can be as high as 1500 bar, ensures that the molten plastic is pushed into every part of the mold. This helps to reduce cycle times and prevent surface defects such as shrinkage, warping and short shot.
A built-in cooling system is essential for reducing cycle times and enhancing the quality of the finished part. The molded plastic must be sufficiently cooled before it can be ejected from the mold. During the cooling phase, holding pressure (slightly lower than injection pressure) is applied to compensate for shrinkage while the molded plastic solidifies. Depending on the size and complexity of the part, cooling can take anywhere from a few seconds to several minutes.
Injection molded parts are often made from thermoplastic polymers that are blended with other materials for added strength and tensile strength. Common additives include carbon black for improved abrasion resistance and zinc oxide to increase corrosion protection. These materials are also available in a variety of colors to suit the visual requirements of the final product.
Once the molded plastic has cooled and solidified, it is ejected from the mold using a retractable tool. The sprue, which is the main channel through which the plastic is injected into the mold, and the gates, which direct the flow of molten plastic to each cavity, must be precisely calibrated to ensure that all of the cavities are filled properly. This is vital for reducing the weight and volume of the finished part and improving aesthetics.
Thermosetting Polymers
Polymers are fundamental to modern manufacturing, providing the backbone for countless automotive and consumer electronics industries. Two types of polymers in particular – thermoset and thermoplastic – have specific characteristics that differentiate them and make them unique within the injection molding world.
Thermosetting polymers are cured by applying heat to the polymer pellets, which causes chemical reactions that increase cross-linking between polymer chains. Once these reactions are complete, the polymer becomes hard and unbreakable. Thermosetting plastics are also insoluble in ether, making them ideal for injection molding applications.
These polymers are commonly used in the production of car parts such as brake pistons, as well as electrical components like wire insulation and circuit boards. They are known for their resistance to elements such as electricity, water and heat, which helps ensure safety and reliability in demanding environments.
Injection molded thermoset polymers are commonly used in the production of appliances and consumer goods such as kitchen utensils, toaster handles, and bathroom fixtures. These products are able to provide a number of advantages aesthetically, structurally and economically when compared to other materials such as metals and woods.
When comparing thermosets to other injection molding materials, their most notable differences are how they respond to heat and their strength. Thermosetting polymers cannot be re-melted, which makes them difficult to recycle into new plastics. This is in stark contrast to thermoplastics which can be re-melted and reshaped once they have cooled.
Thermosets are also much less flexible than other plastics. This is because they have a higher viscosity than other plastics. Because of this, they must be injected into a mold with a lower pressure to maintain their shape. This makes them more difficult to handle than thermoplastics, and requires a more sophisticated injection process to be created.
Thermosetting plastics are expensive to produce due to the costs of a precision-crafted mold. Additionally, they require a much longer cooling time than other plastics. Because of this, thermosets are not ideal for small runs and are typically only produced in large quantities.
Thermoplastic Molding Process
Thermoplastic molding is used to produce a range of products, from small components to large objects. The process supports high production volume and is well suited to applications with stringent requirements, such as medical devices. Injection molding is also ideal for making items with intricate details, such as pocket combs and automotive dashboards.
Before injection, thermoplastic pellets are treated to ensure optimal performance. The pellets are melted and propelled into a mold cavity using high injection pressure. The pressure and speed are calibrated to replicate the mold’s shape and surface finish, while minimizing shrinkage and warping.
During the injection phase, the liquid plastic fills every part of the mold to create a finished product. Injection speed, which depends on the complexity of the part, influences the filling pattern and appearance. Once the plastic is injected, it undergoes a cooling process facilitated by the mold’s built-in coolant system. During this time, holding pressure (slightly lower than injection pressure) is applied to help compact the molded plastic and compensate for shrinkage.
To avoid defects, it is important to follow proper injection molding design guidelines. These include specifying bosses or threaded inserts for fasteners, rounded edges, ribbed supports for extra strength, snap-fit joints or friction fits as joining features, living hinges to allow for some flexibility, and draft angles on vertical walls to prevent wall deformation.
Once the injection process is complete, the molded plastic is allowed to cure before being separated from the tooling. The part is then finished with additional operations like polishing or laser etching to achieve the desired look and feel.
There are a variety of polymers that can be injected, including all thermoplastics and many thermosets. However, the most commonly used polymers in injection molding are polyethylene and polystyrene. Both are affordable, durable, and highly versatile. Polyethylene, in particular, has high tensile strength and good ductility, making it an excellent choice for injection-molded parts like trays and storage containers. It is also resistant to impact, heat, and moisture absorption.
Thermosetting Molding Process
Thermosetting plastics are a great option for high-volume programs that require strong, durable materials. They have good resistance to heat, chemical degradation and physical wear. They are also able to withstand repeated reshaping, unlike thermoplastics, which cannot be re-melted. They are typically stored as pellets before injection molding.
The process for thermosetting plastic injection molding is very similar to that of thermoplastic injection molding. The polymer is placed in a heated barrel where it reduces its viscosity before being injected into the mold. The pressure applied during the injection molding process creates a chemical cross-linking that results in the hardened product. Once the part has cured, it is cooled and ejected from the mold.
This is a very fast process compared to the other injection molding processes. It can reach a cycle time of just 10 to 120 seconds, depending on the type of polymer used. A faster cycle time means that more parts can be produced in a shorter amount of time, which can save money on labor and machine costs for your production line.
Another advantage of thermoset injection molding is that it does not have to be preheated. The material is loaded into a transfer pot, which usually resides above or as part of the upper mold half, where it is sealed. A transfer ram extends, forcing the plastic from the pot into the mold cavity. The force of the ram can be increased to increase the flow rate of the plastic into the mold. During this process, the plastic is mixed with fillers to achieve desired properties such as low shrinkage, strength or other specific characteristics.
The main drawback of this molding method is that the material must be kept at a low viscosity while it is being injected into the mold. This requires a well-sealed mold and the use of accurate processing software to ensure that the rheokinetic behavior is correctly represented. This is particularly important for thermosets, where the resulting cross-linking reaction can significantly alter the fluidity of the material.
Thermosets are usually filled with additives to improve their properties, such as reducing the cost of the plastic or making it more resistant to corrosion, impact or other factors. This can result in a very wide range of viscosity, which in turn can make it difficult to control with an injection molding machine.